Latest Sectors News
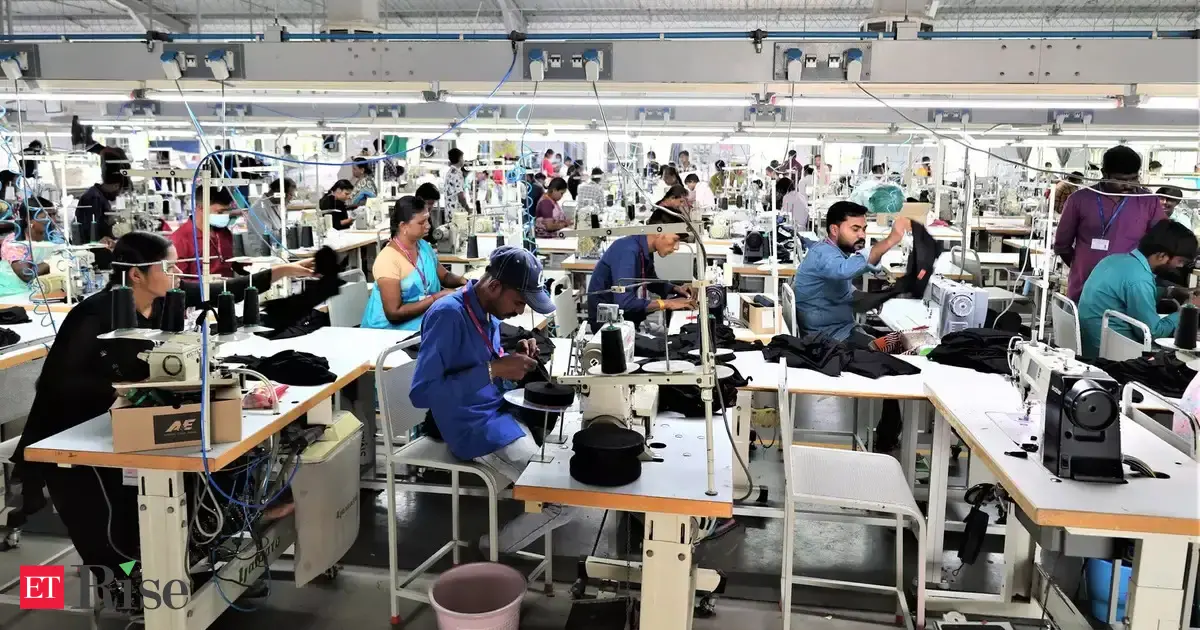
Despite churning out impressive trade numbers, Tiruppur is plagued by various problems that threaten its very survival. Addressing key issues of labour, tech, infrastructure and capital is the only way forward to make this cluster thrive. In the first of a three-part series, ET Digital brings an in-depth ground report from the textile heartland. View More
Tucked away on the banks of the Noyyal River in Western Tamil Nadu, Tiruppur, at first glance, may appear to be a quiet, nondescript town. Its modest appearance, however, belies its status as a heavyweight in global textiles. But the numbers say it all. The textile cluster generated a whopping Rs 70,000 crore in total trade in FY25. In fact, Tiruppur accounts for 90% of India’s cotton knitwear exports and 54% of overall knitwear exports, earning it the distinction of the ‘Knitwear Capital of India’. Not just in the last fiscal year, Tiruppur has been consistently contributing more than half to India’s total knitwear exports over the past several years. In FY25, it achieved a record export of Rs 39,618 crore in knitwear products, an increase from Rs 33,045 crore in FY24 and Rs 27,280 crore in FY20, according to data from the Ministry of Commerce and Industry ( see chart ). Despite its remarkable growth over the years, Tiruppur faces significant challenges. Until recently, the absence of a level playing field with nations like Bangladesh, which benefits from duty-free access in textiles as a Least Developed Country (LDC), made exports in Tiruppur highly uncompetitive. Although the recent political instability in Bangladesh and the China+1 strategy presented growth opportunities, with global clothing brands shifting their focus to India, it was short-lived. Despite its remarkable growth over the years, Tiruppur faces significant challenges of infrastructure, capital and labour which make it less competitive. An in-depth conversation with a cross-section of industry players during ET Digital ’s recent visit to Tiruppur reveals that addressing the issues of skilled labour availability, infrastructure improvements, and investing in technology upgrades is vital to the future prospects of Tiruppur. But before we dive in, let’s take a trip down memory lane. Live Events Creating An Ecosystem The initial exports (direct) from Tiruppur started with Italy. Verona, an Italian garment importer, came to the city in 1978 through Mumbai exporters to purchase white T-shirts. At that time, a lot of workers were engaged in manufacturing garments for merchant exporters. Seeing the potential, Verona brought European business to Tiruppur, according to the Tiruppur Exporters Association ( TEA ). Three years later, the European retail chain C&A entered the market, followed by other stores who approached exporters for garment supplies. Eventually, exports from Tiruppur started in the 1980s with 15 export units. In 1985, the city exported garments worth Rs 15 crore. “In the past, we did not have the technology for dyeing, and we needed water; neither did we know the technology for converting the grey fabric into colour,” remembers Kumar Duraiswamy , Joint Secretary of TEA. “All these were developed by our own R&D.” Initially, Tiruppur produced only white fabric. As buyers wanted more colours, they sourced the dyes from Ahmedabad and the northern parts of the country. “We initially dyed it in an iron drum, later upgraded to a tile tank, and subsequently evolved to a steel tank. Then machines from Europe, the US, Taiwan, and Japan replaced this steel tank,” he adds. The next couple of years were a windfall, with exports from the cluster touching Rs 300 crore in 1990. In FY25, the number scaled to a record Rs 40,000 crore, while the domestic consumption grew to an impressive Rs 30,000 crore. Currently, the Tiruppur textile cluster houses more than 20,000 units. Among these, over 2,500 units engage in knitting, more than 11,100 units handle sewing jobs & other ancillary tasks, and over 2,500 produce garments for exports; collectively, these units directly employ over 600,000 workers. ET Online As business continues to expand, Tiruppur also encounters challenges that emerge along the way. A Knotty Problem Technological upgrade is one of the biggest challenges facing the textile sector. According to experts and industry players, Tiruppur, the country’s largest textile cluster, needs a technological upgrade to compete with global peers. “We need at least 50% capex for the upgradation of technology,” says Thirukkumaran Natarajan , Chairman of Esstee Exports India and General Secretary of TEA. Another hurdle is size. The Tiruppur textile cluster comprises mostly MSMEs. Currently, among the 2,500 exporters in the city, the top 100 generate business totalling Rs 20,000 crore, while the remaining 2,400 account for the balance of Rs 20,000 crore. “These 100 big exporters are doing fairly well,” says Duraiswamy, as they can foresee the market over the next 20 years and are improving their offerings while monitoring their competitors. “However, those [smaller] units that cannot observe these aspects or fail to keep up with the competition are still trailing as far as growth is concerned,” he adds. In textiles, Bangladesh and China are the main competitors of India. “The government offers full subsidies in Bangladesh, unlike in India, where we don’t get such kinds of subsidies here,” says Siva Subramaniam , Founder & Chief Executive of Raft Garments, a second-generation manufacturer and exporter of sustainable T-shirts, intimate wear and sweaters from Tirupur, which, according to him, makes it difficult for Indian exporters to compete with counterparts. Technological upgrade is one of the biggest challenges facing the textile sector. According to experts, Tiruppur needs a technological upgrade to compete with global peers. The labour shortage is one more factor that has impacted MSME growth in Tiruppur. Last year, there was a shortage of 100,000-150,000 labourers, as migrant workers who returned to their home states to cast votes in the Lok Sabha elections were reluctant to come back. The workers believed they would secure jobs in their home states. In fact, labour is more expensive here, says Subramaniam, making it challenging for exporters to compete with other countries. “While wages hover between Rs 8,000 and Rs 10,000 per month in Bangladesh, in India it easily ranges between Rs 15,000 and Rs 18,000 per month,” he says. Subramaniam also highlights the need for an improvement in infrastructure to attract more international buyers. “We don’t have direct access to the airport. Buyers from New York or London must first travel to Chennai or Mumbai. From there, they take a flight to Coimbatore and then drive to the factories in Tiruppur. So, it is quite arduous for them to plan a visit.” While the government has announced various schemes to uplift the textiles sector, they have yielded limited benefits so far, especially for MSMEs in Tiruppur. For instance, the National Technical Textiles Mission (NTTM). The initiative was launched in 2020 with the government allocating Rs 1,480 crore for the FY21-FY26 period. However, only Rs 509 crore has been spent as of January 1, 2025, which points to the need for further efforts to elevate the prominence of clusters like Tiruppur as a global knitwear hub. ET Online Another government initiative is the Technology Upgradation Fund Scheme (TUFS). It was first launched in 1999 by the Ministry of Textiles as a credit-linked subsidy scheme intended for the modernisation and technological upgradation of the textile industry in the country. It was discontinued in 2010, and the government launched the Restructured TUF Scheme (RTUFS) in 2011. Over the years, the scheme showed up with different names, such as the Modified Technology Upgradation Fund Scheme, the Revised Restructured Technology Upgradation Fund Scheme (RRTUFS), and the Amended Technology Upgradation Fund Scheme (ATUFS) in 2016, which was valid till March 2022. However, there has been no update on this scheme since then. The scheme was an important tool helping the textiles industry expand into domestic and global markets by funding technology upgrades, quality production, and efficiency, thereby improving competitiveness. The scenario is comparable for the much-publicised Production-Linked Incentive (PLI) scheme for textiles, which seeks to promote the production of man-made fibre (MMF) apparel, MMF fabrics, and technical textile products in the country. The scheme requires a minimum investment of Rs 100 crore and a minimum turnover of Rs 200 crore per company. “The terms and conditions of the PLI, as per Duraiswamy, are ‘Greek and Latin’ for smaller players. “The PLI scheme is only for 3-4% of the industry; the rest cannot comply,” he says. Natarajan of Esstee Exports India concurs, saying that the Rs 100 crore investment is intended for a large format industry focused on MMF. Tiruppur has traditionally relied on cotton, and only recently has there been some scope emerging for MMF. “We are lacking in quality of fibre as well as technical expertise. Moreover, this (Tiruppur) is a cluster where MSMEs thrive; it is not for large-format industries, and the schemes need to be in accordance with such small enterprises. It is difficult for an MSME to invest Rs 100 crore,” he explains. “Most companies in Tiruppur are family-run and lack a corporate structure, limiting their ability to scale like international counterparts. Besides this, factors such as dependence on buying houses play up, as a significant portion of orders comes through intermediaries rather than direct brand collaborations, which reduce control over pricing and market positioning,” says Devroop Dhar, MD & Co-founder of Primus Partners. Phone calls and emails sent to both the state and central textile ministries regarding the challenges facing the Tiruppur cluster went unanswered till the time the story was published. Untangling the Threads However, not all is bleak. Schemes such as the Rebate of State and Central Taxes and Levies (RoSCTL) and the Samarth Scheme for skill development have proven beneficial. Bharat TEX 2025, held in the capital in February, also provided more business and networking opportunities for exporters in Tiruppur. In addition, the recent India-UK free trade agreement has got exporters anticipating brighter times ahead. There’s a caveat, though. “It will help us, but to leverage this opportunity further, we need to get upgraded technologically and financially. More government support can help us double our current turnover in exports to Rs 80,000 crore by 2030,” Natarajan adds. A more specialised focus on MSME units, as per Duraiswamy, can make all the difference for clusters like Tiruppur. “The government needs to consider having a technology upgradation fund, especially for the smaller units to survive and thrive,” he says. While government initiatives like Samarth can be helpful for addressing skilled labour shortages, Dhar suggests the establishment of specialised training centres at major textile hubs to ensure a steady supply of skilled workers, thereby reducing dependency on untrained labour and improving overall productivity. Additionally, he underscores the pivotal role of the government in aggregating MSMEs, like the support provided to small farmers via farmer producer organisations (FPOs) in the agriculture sector. “By facilitating the formation of MSME clusters and cooperatives, the government can help small businesses negotiate directly with buyers, ensuring better pricing, market access, and supply chain efficiency.” The labour shortage is one more factor that has impacted MSME growth in the textile cluster. Last year, there was a shortage of 100,000-150,000 labourers. Experts recommend that the government draw insights from competitors to improve the attractiveness of domestic textiles. Cities like Guangzhou, Shanghai, and Shenzhen are leading due to their advanced infrastructure, proximity to major ports, and established supply chain networks that support their progress. A lot of global capacity in China got built since the government invested in the sector, says Anand Ramanathan, Partner and Leader, Consumer Products & Retail Sector, South Asia, Deloitte India. “They (China) built facilities at scale. [But,] if you look at Tiruppur, it is still very sub-scale. In China, for instance, one can see specific regions that specialise in manufacturing a particular type of product. Hence, at that scale, cost economics really falls,” he explains. While a lot of effort in India is going towards semiconductors, with the government competing for land and giving access to capital to attract semiconductor manufacturing in the country, Ramanathan notes that similar efforts have not been taken towards the apparel and textile industry. “It has never really happened at that scale for them. This is one area where the sector has not got its act together.” So, what is the way forward, and how can clusters like Tiruppur leverage their unique strengths? Ramanathan states that subsidising manufacturing capacity, upgrading technology and ensuring capital availability can significantly alter the landscape. “Capital is still very scarce (here). Globally, lower interest rate regimes like Japan have credit available aplenty. We need to think about how to replicate some of that, especially in manufacturing, given our scarcity,” Ramanathan highlights. The government has set an ambitious target of $100 billion for textile export by 2030, up from $36.6 billion in FY25. Tiruppur, as the largest textile cluster in the country, has a bigger role to play in it. As TEA’s Duraiswamy puts it, “This is the right time for India. In the next 20 years, we can grow the textile industry across the globe. However, without the help of the government, this is not at all possible,” he says. Illustrations by Garima Bora.